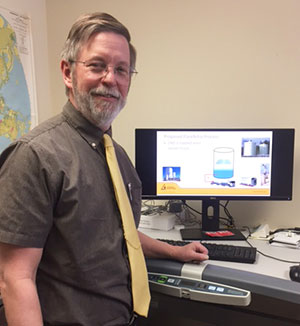
Contact Us
Institutional Communications
Bureau of Mines Building, Room 137
Laramie, WY 82071
Phone: (307) 766-2929
Email: cbaldwin@uwyo.edu
Published March 11, 2020
Two University of Wyoming engineering professors recently received a provisional patent for a method, using cryogenic transport, to help the oil and gas industry reduce emissions created by flaring and venting of natural gas.
Brian Toelle, a professor of practice in UW’s Department of Petroleum Engineering, and Maohong Fan, a UW School of Energy Resources professor in chemical and petroleum engineering, received a patent for their FlareNitro process. Fan recently was named to Clarivate Analytics’ list of highly cited researchers in 2019 in the field of chemical and petroleum engineering.
Over the years, capturing produced gas has proven to be economically and technically challenging for the oil and gas industry. One possible solution is the liquefaction of natural gas at the well site, Toelle says.
“Produced or solution gas comes out of solution when oil is produced in some geologic plays, like the Bakken in North Dakota. If there is no pipeline nearby, it is often flared so the oil can be produced,” Toelle says. “This can be both wasteful and harmful to the environment. The FlareNitro process uses cryogenics to create and transport the gas-to-liquid form when a gas pipeline is not available.”
Gas flaring refers to the combustion of associated gas generated during various processes, mainly oil recovery. The typical flare used in the gas industry is composed of a boom or stack that collects the unwanted gases to be flared.
Toelle says their process is currently in the conceptual phase, but would work like this: At the well site, produced gas is gathered and stored at the well location. Liquid nitrogen is then transported from a nearby facility by tanker truck. A FlareNitro reaction vessel also is taken to the well site and charged with liquid nitrogen. The internal temperature inside the reaction vessel would be brought to less than minus 320 degrees Fahrenheit.
The natural gas stored on-site would then be flowed into the reaction vessel, where it would condense and be collected as liquefied natural gas (LNG), which is then loaded onto another tanker truck. The LNG tanker truck would then be driven to a nearby pipeline and off-loaded.
“Once in operation, a FlareNitro regional base could be set up in various locations where high gas-to-oil ratio oil reservoirs are being produced,” says Toelle, who spent 34 years in the oil and gas industry working for Texaco, Saudi Aramco and Schlumberger. “One of these regional bases could service the well sites for multiple operators in the area.”
While waiting for pipeline to be constructed at the well site, a FlareNitro service could gather all of the natural gas that would normally be flared or vented, he says, which would allow the operator to obtain financial benefit from the produced gas that would normally be flared. This also would result in more environmentally friendly operations at the location.
“The FlareNitro process shifts the energy input for this from the well location to a liquefaction center,” Toelle says. “This means the need for a fuel source at the well location is decreased, if not eliminated.”
Toelle and Fan worked approximately nine months on the project before securing a provisional patent. The idea came out of government concerns about flaring. In addition to flaring being wasteful, many environmentalists see it as an air pollution problem and contributing to climate change.
“This came to my attention during a visit to the Department of Energy in Washington, D.C. I was with a group of visitors to the Department of Energy when they indicated that this was a priority for them,” Toelle explains. “They released a request for research proposals on this subject at the same time.”
The flaring of natural gas occurs in many producing basins within the U.S., including the Bakken in North Dakota and the Permian Basin in west Texas, Toelle says. Additionally, many countries around the world have associated gas flaring -- they have to conduct -- to maintain oil production.
In March 2015, roughly 45 billion cubic feet of natural gas was flared in North Dakota, which is 5 percent of natural gas production, Toelle says.
“Using the largest truck tankers available, this amount of gas would require 3,450 tanker runs to move all of that flared gas,” he says. “With two tanker runs per day, all the gas normally flared in North Dakota could be transported with a fleet of approximately 62 tankers.”
If the FlareNitro process could be proven, this could be a big help to the industry for the flaring and venting of produced gas at the well sites as well as the stranding of producible gas fields, which are economically too far away from existing pipelines. Toelle adds that the amount of money an operator could save using the FlareNitro process “depends on the company and the geologic play.”
Toelle and Fan are seeking roughly $160,000 in funding over two years from the industry to help bring their concept to reality. This amount includes funding for a research assistant, materials, and manufacturing and fabrication of materials.
“Only a few key technologies still need to be researched in order to produce FlareNitro as a viable service. This will include what materials the reaction chamber needs to be composed of and what configuration,” Toelle says. “Additionally, we need to produce research on what type of insulation is needed in order to maintain a good energy balance and keep the system economic.”
Contact Us
Institutional Communications
Bureau of Mines Building, Room 137
Laramie, WY 82071
Phone: (307) 766-2929
Email: cbaldwin@uwyo.edu